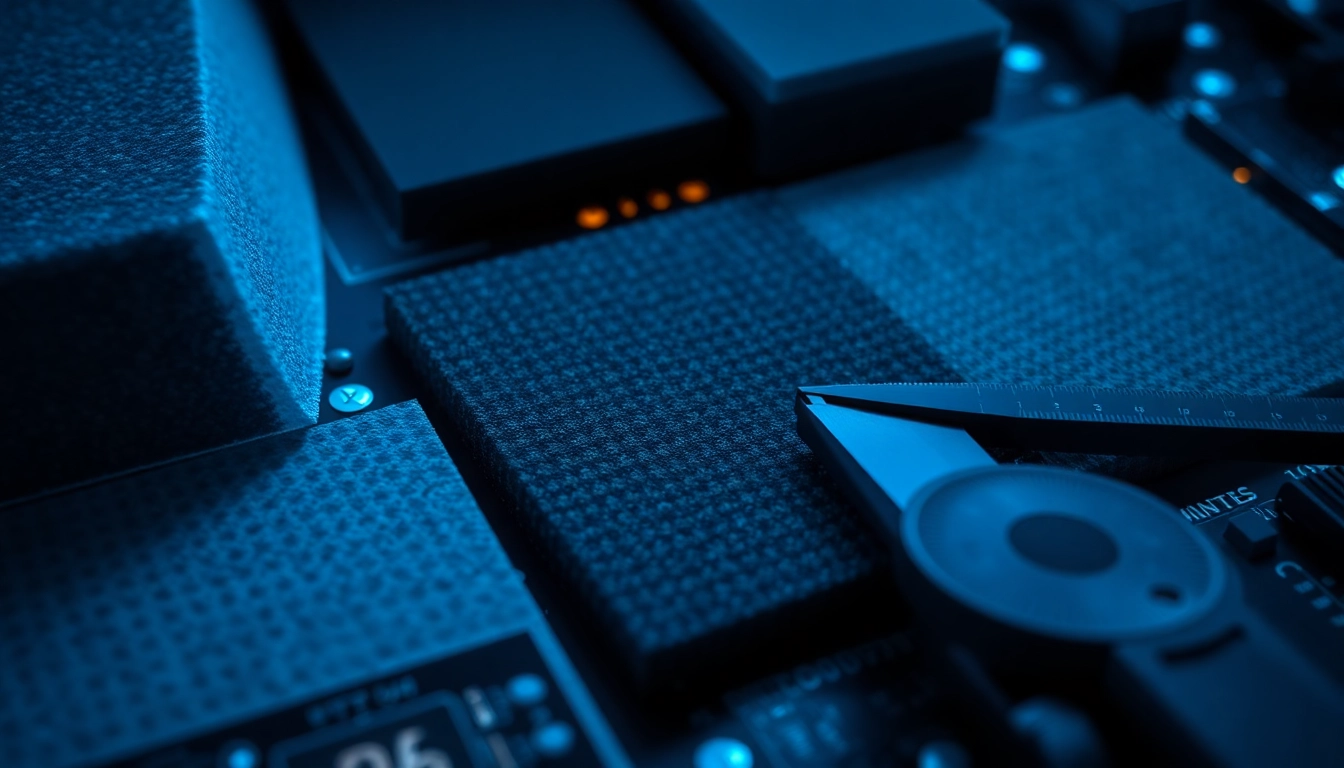
Understanding Thermal Management Materials
What Are Thermal Management Materials?
Thermal management materials refer to a broad spectrum of products specifically engineered to regulate temperatures in various electronic devices and applications. As technology advances, the need for efficient heat dissipation becomes increasingly crucial, particularly in high-performance electronics where overheating can lead to severe performance issues or even failure. Among these materials, we find thermal interface materials (TIMs) that facilitate heat transfer between components, as well as advanced substances like phase change materials and thermal conductive adhesives. Effective thermal management materials ensure that electronic devices operate within safe temperature ranges, improving reliability and extending the lifespan of the equipment.
The Importance of Heat Dissipation in Electronics
As electronics become more compact and powerful, managing heat dissipation has emerged as a critical aspect of design and engineering. Overheating can cause numerous problems, including reduced efficiency, unpredictable behavior, and permanent damage to electronic components. Efficient thermal management systems facilitate the quick removal of excess heat, ensuring that components maintain optimal operating temperatures. This is especially vital in sectors like telecommunications, computing, and automotive engineering, where device reliability can significantly influence performance and safety.
Types of Thermal Management Materials
Thermal management materials can be categorized into several key types, each serving distinct functions in dissipating heat:
- Thermal Interface Materials (TIMs): Essential for maximizing thermal conduction between heat-generating components and heat sinks.
- Phase Change Materials (PCMs): These materials absorb heat while undergoing a phase change, useful for peak load shifting in thermal management.
- Gap Fillers: Used to fill air gaps between components, enhancing thermal conductivity and ensuring surfaces make better thermal contact.
- Thermal Adhesives: Combining bonding and thermal conductivity properties, these materials are crucial in device assembly and performance.
- Heat Spreaders: Often made from metals like copper or aluminum, they transfer heat effectively over a wider area.
Key Applications of Thermal Management Materials
Electronics Cooling Solutions
In electronic applications, thermal management materials are vital for managing the heat produced by processors, graphics cards, and other high-performance components. Examples include the use of thermal interface materials between CPUs and heatsinks or using thermal pads in GPUs. By ensuring efficient heat transfer, manufacturers can improve performance and extend the lifespan of electronic devices while maintaining compact designs.
Automotive Thermal Management
In the automotive sector, effective thermal management is essential for engine cooling systems, battery thermal management in electric vehicles, and overall vehicle performance. Materials such as phase change materials and thermal barrier coatings are employed to regulate temperatures, ensuring that components function effectively while minimizing energy loss and enhancing fuel efficiency.
Aerospace and Defense Applications
Thermal management materials play an important role in aerospace and defense technologies, especially in high-stakes environments where reliability is paramount. From managing the heat generated in turbines to thermal insulation in spacecraft, advanced materials are used to protect sensitive components from extreme temperature variations, thus ensuring operational efficiency under stress.
Selecting the Right Thermal Management Materials
Material Properties to Consider
When selecting thermal management materials, engineers must evaluate several critical properties:
- Thermal Conductivity: The ability of a material to conduct heat, measured in watts per meter kelvin (W/mK).
- Viscosity: For materials intended to be applied as adhesives or gels, the viscosity affects application ease and effectiveness.
- Thermal Stability: The ability of a material to maintain its characteristics across a range of temperatures.
- Mechanical Properties: Important for ensuring durability within the intended application, especially in high-stress environments.
- Electrical Properties: Ensuring the selected materials do not conduct electricity is critical for many electronic applications.
Performance Metrics and Standards
Performance metrics for thermal management materials vary by application but generally include thermal resistance, interface pressure, and reliability over time. Standards and testing protocols, such as those set by ASTM International, guide manufacturers in gauging material performance under different conditions. Ensuring compliance with industry standards, such as IPC (Institute for Printed Circuits), can define product quality globally, which is crucial for manufacturers aiming for regulatory approvals.
Common Challenges in Material Selection
Selecting thermal management materials can pose unique challenges, including:
- Compatibility Issues: Some materials may interact poorly with other components, affecting performance or long-term reliability.
- Cost Considerations: High-performance materials can be more expensive, prompting a need for balance between cost and performance.
- Material Thickness: Thicker materials may offer enhanced performance but can affect space and weight constraints in device design.
- Environmental Concerns: With increasing scrutiny on materials affecting ecological sustainability, manufacturers must consider biocompatibility and recyclability.
Best Practices for Implementing Thermal Management Solutions
Steps to Optimize Heat Transfer
To implement effective thermal management solutions, following these steps can optimize heat transfer:
- Conduct a Thermal Analysis: Understand the thermal profile of your application to identify hotspots.
- Select Suitable Materials: Match the thermal management materials to the specific requirements of your application.
- Ensure Proper Installation: Follow manufacturer guidelines for applying thermal interface materials to ensure optimal performance.
- Monitor Performance: Utilize thermography and other monitoring tools to measure performance and detect inefficiencies.
Case Studies on Successful Applications
Examining real-world applications illustrates the significance of thermal management materials. For instance, in the consumer electronics sector, leading manufacturers have employed advanced thermal pads in smartphones to manage heat. By integrating these materials, they observed marked improvements in performance under heavy usage, leading to higher consumer satisfaction and reduced failure rates. Additionally, automotive manufacturers implementing phase change materials in battery systems have shown enhanced thermal regulation, promoting efficiency and safety in electric vehicles.
Future Trends in Thermal Management Technology
Innovation in thermal management is ever-evolving, with promising trends on the horizon. Emerging materials such as graphene and aerogels offer exceptional thermal properties and lightweight solutions. Moreover, the integration of electronic devices into IoT (Internet of Things) necessitates efficient cooling solutions for compact, high-density packaging. Enhanced modeling and simulation techniques, including computational fluid dynamics (CFD), will likely play a larger role in predicting thermal behavior and refining material selection.
Resources and Further Reading on Thermal Management Materials
Research Papers and Technical Resources
A wealth of research papers and technical resources is available for professionals seeking to delve deeper into thermal management materials. Journals such as the Journal of Electronic Materials and Thermal Science and Engineering Progress regularly publish studies highlighting advancements in materials, applications, and theoretical modeling.
Videos and Tutorials on Material Applications
Visual learning through online platforms like YouTube can provide insight into practical applications of thermal management materials. Tutorials often exhibit material application techniques and comparisons of performance metrics in real-time scenarios.
Frequently Asked Questions Regarding Thermal Materials
As interest in thermal management materials grows, so do the questions surrounding their properties and applications:
- What are the differences between TIMs and gap fillers? TIMs facilitate direct heat transfer between components, while gap fillers are used to enhance contact and thermal conduction over uneven surfaces.
- How can I improve the thermal conductivity of my assembly? Consider employing higher-grade thermal interface materials or reducing air gaps between heat-generating components and heat sinks.
- What regulatory standards apply to thermal management materials? Standards vary by industry but often include ASTM and IPC certifications related to material composition, performance, and environmental impact.