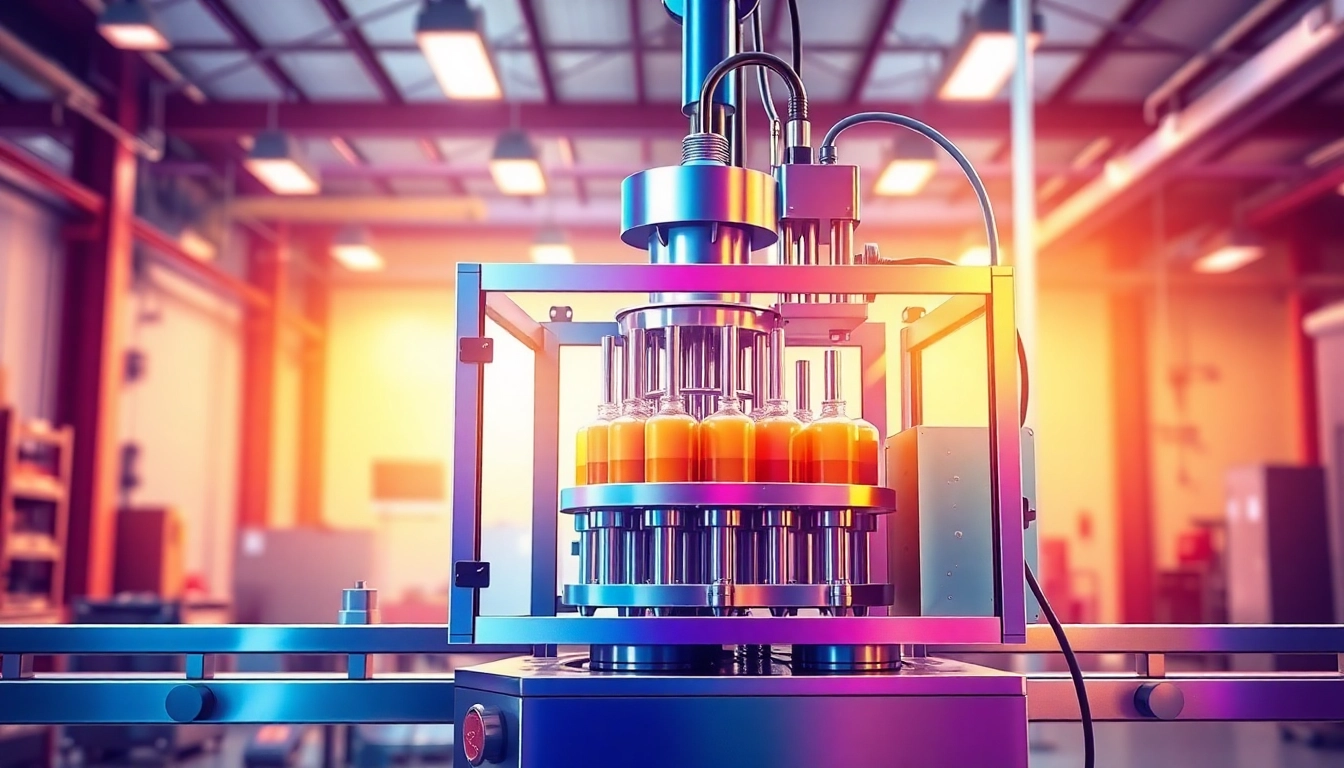
Understanding Filling Machines
Filling machines are crucial components in the packaging industry, employed across a myriad of applications—from food and beverage to pharmaceuticals and cosmetics. Their primary function is to accurately dispense the desired quantity of liquid, granulated, or powdered product into containers, thereby streamlining the production process and ensuring product integrity. In today’s marketplace, Filling Machine technology has advanced significantly, giving rise to a range of types suitable for various industry needs, from simple manual systems to complex automatic solutions that integrate seamlessly into larger manufacturing systems.
Types of Filling Machines
Filling machines can be categorized based on different criteria, primarily by their operational mechanisms and the level of automation involved. Here are the most common types:
- Manual Filling Machines: These require human intervention for operation and are best suited for small-scale production or artisanal applications. They are typically cost-effective and easy to operate but can be time-consuming.
- Semi-Automatic Filling Machines: These machines automate certain processes while still requiring some degree of human operation. They are ideal for medium-scale operations and provide increased efficiency compared to manual machines.
- Fully Automatic Filling Machines: These sophisticated systems are designed for high-volume production environments. They drastically reduce labor costs and human error, offering the best option for large-scale manufacturers.
- Volumetric Filling Machines: Utilizing a system of pumps and valves, volumetric fillers measure liquid by volume. They are highly accurate and widely used in various industries including food and pharmaceuticals.
- Pneumatic Filling Machines: Relying on air pressure to dispense and fill products, these machines are particularly effective for filling viscous liquids and are a popular choice in food production.
How Filling Machines Work
Understanding the operational mechanics of filling machines helps businesses optimize their production processes. Here’s a general overview:
- Container Placement: The filling process begins with the precise positioning of containers under the filling nozzle, often utilizing conveyor belts to facilitate movement.
- Filling Mechanism Activation: Depending on the machine type, the filling process is activated either manually or automatically through programmable controls or sensors.
- Measurement of Product: Using various measurement systems—like volumetric measures or weight—the machine dispenses product into the container, ensuring the correct volume or weight.
- Nozzle Control: Nozzles are activated to control the flow of product, with options for anti-drip mechanisms to prevent spillage and maintain cleanliness.
- Container Ejection: Finally, filled containers are ejected onto the next phase of production, whether that be capping, labeling, or packaging.
Key Features to Consider
When selecting a filling machine, certain features should be prioritized to meet operational standards and product requirements:
- Speed and Capacity: Evaluate the machine’s filling speed and the volume per cycle to ensure it meets your production demands.
- Accuracy: The precision of the filling volume is crucial, particularly in industries like pharmaceuticals and cosmetics where regulations are stringent.
- Versatility: Consider whether the machine can handle various types of products (liquids, powders, granules) and different container sizes.
- Ease of Cleaning and Maintenance: Machines that are easy to clean can reduce downtime and keep operations running smoothly.
- Integration: The ability to integrate the filling machine into existing production lines or software systems is crucial for seamless operations.
Benefits of Using a Filling Machine
Employing filling machines in production offers a myriad of benefits that can enhance the efficiency and effectiveness of your operations:
Increased Production Speed
Filling machines significantly enhance production speed by automating the filling process. Where human labor may take considerable time to complete a task, machines can fill hundreds or even thousands of units within the same timeframe, thereby accelerating the entire production process.
Enhanced Accuracy and Consistency
Precision is paramount in production; filling machines enhance product consistency, minimizing the risk of human error. Automated systems ensure that every bottle or container receives the exact amount required, which is particularly vital in industries like pharmaceuticals, where discrepancies can have serious implications.
Cost Savings Over Time
While the initial investment in a filling machine can be significant, the long-term savings on labor, reduction of waste due to inaccuracies, and increased production speed can offset these costs. Additionally, many machines offer programmable functions, further enhancing productivity and reducing the potential for costly downtime.
Selecting the Right Filling Machine
The selection of a filling machine tailored to your specific needs is critical for maximizing operational efficiency and effectiveness. Here’s a structured approach to making the right choice:
Requirements Based on Product Type
Understand the nature of the product you need to fill (liquid, powder, or granulated) as well as its viscosity and particulate content. Different types of products often require specific types of filling machines to ensure optimum performance. For instance, viscous products may require a pneumatic filler, while powders are best suited for auger fillers.
Evaluating Automation Levels
Consider your current operational needs and future growth plans. Automated systems provide numerous advantages, but they require a higher upfront investment. Assess whether a semi-automatic system meets your needs or if fully automatic machinery is warranted for your production scale.
Budget Considerations
The budget for your new filling machine should include not just the purchase price, but also installation, training, and maintenance costs. Ensure you conduct a cost-benefit analysis to understand the return on investment (ROI) associated with different options.
Maintenance and Support for Filling Machines
Proper maintenance is crucial for ensuring the longevity and effectiveness of your filling machines. Routine checks and servicing can prevent minor issues from evolving into major problems.
Regular Maintenance Best Practices
Implementing a comprehensive maintenance schedule can greatly enhance the operational reliability of your filling machinery. Key practices include:
- Routine inspections of mechanical components and electrical systems to detect wear and tear early.
- Regular cleaning schedules to prevent buildup of product residues and contaminants.
- Calibration checks for accuracy in measurement systems, which ensures the filling process remains within specified tolerances.
Common Issues and Troubleshooting
Being prepared for common fill machine issues—such as underfilling or overfilling, nozzle clogs, and equipment jams—can save considerable time and resources:
- Underfilling or Overfilling: Regular calibration and ensuring that the machine parameters match the product specifications can often resolve these issues swiftly.
- Jamming or Clogging: Regular inspections and cleaning can prevent this; using quality product materials also reduces clogs significantly.
Service and Warranty Options
When investing in filling machines, it’s advisable to consider the warranty and service options provided by the manufacturer. Comprehensive service packages might include maintenance support, which can be crucial in ensuring minimum downtime during production runs.
Future Trends in Filling Machine Technology
As technology continues to evolve, so do the capabilities and applications of filling machines. Keeping an eye on emerging trends can provide a competitive edge:
Smart and Automated Solutions
The advent of IoT and smart technology allows for more sophisticated filling machines that can be remotely monitored and adjusted, leading to greater efficiencies and lower operational costs. Data collected can also help refine the production process over time through more informed decision-making.
Sustainability and Eco-Friendly Innovations
With a growing emphasis on sustainability, many manufacturers are developing machines that minimize waste, optimize energy consumption, and use biodegradable materials in production. Transitioning to eco-friendly practices can enhance brand reputation and appeal to environmentally conscious consumers.
Integration with Other Production Systems
Advanced filling machines are increasingly designed to integrate seamlessly with other components of a production line, from labeling to packing. This holistic approach improves efficiency, helps to streamline processes, and enhances overall production workflows.