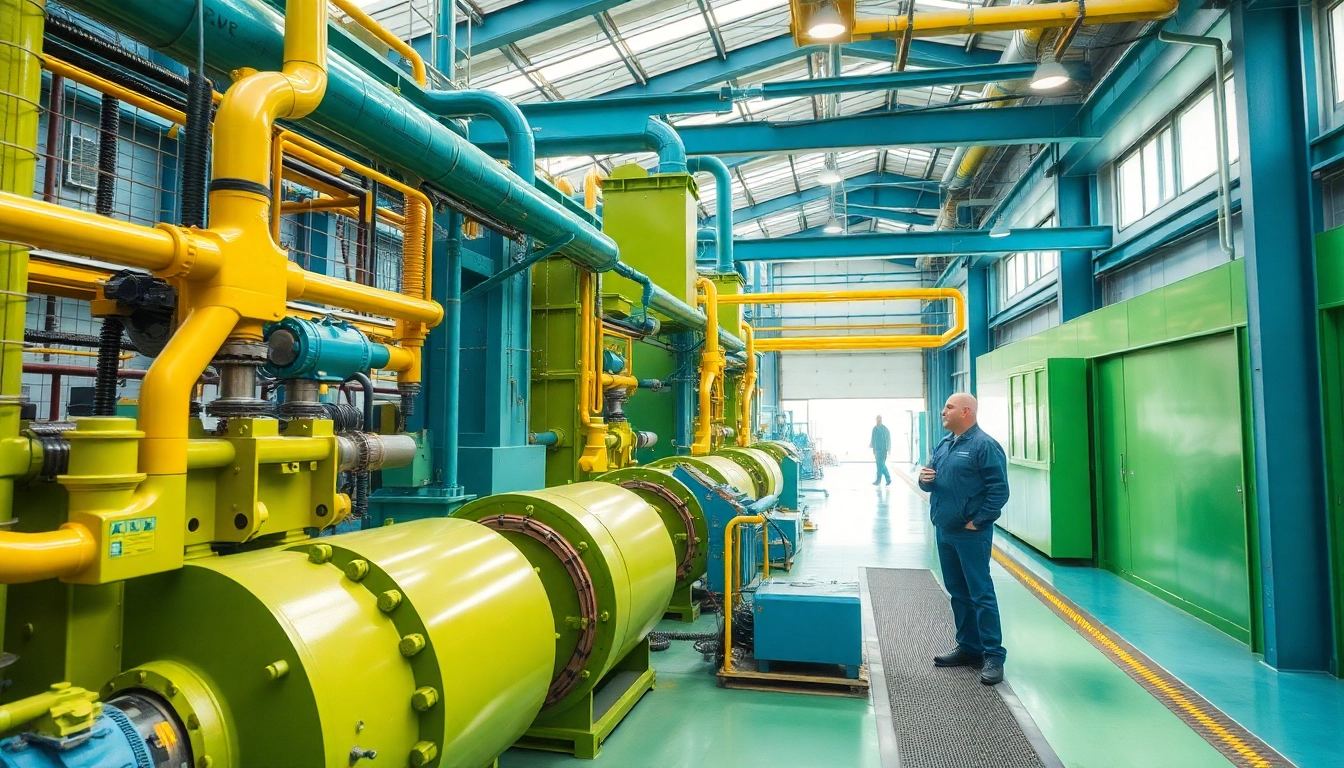
Understanding Ecoating: What It Is and How It Works
Definition and Process of Ecoating
Ecoating, also known as electrophoretic deposition (EPD) or e-coat, is an innovative coating process commonly used for metals and some types of plastics. This method involves immersing the substrate in a solution of paint particles suspended in water, where an electric current is applied. The electrostatic attraction causes the paint particles to be deposited onto the substrate evenly, forming a durable and protective layer. This coating process is celebrated for its ability to deliver consistent thickness even in hard-to-reach areas, making it an ideal choice for complex shapes and geometries often found in automotive and manufacturing applications.
Different Types of Ecoating Methods
There are various types of ecoating methods, each suited for specific applications and requirements:
- Cationic E-Coat: This method utilizes positively charged paint particles, which are attracted to negatively charged substrates. It is favored for its excellent adhesion, corrosion resistance, and uniformity.
- Anionic E-Coat: In contrast, this method employs negatively charged paint particles, often used for specific applications such as metal coatings requiring additional protective measures.
- Hybrid E-Coat: This combines both cationic and anionic features for specialized applications that require unique properties, like higher durability or enhanced aesthetic appeal.
- Epoxy-based E-Coat: Known for superior corrosion resistance, epoxy-based coatings are ideal for industrial applications where durability is paramount.
Benefits of Ecoating for Various Industries
The ecoating process offers numerous benefits that make it a preferred choice across various industries:
- Enhanced Corrosion Resistance: Ecoating provides a robust barrier against moisture and salts, extending the lifespan of coated products, particularly in automotive and construction materials.
- Environmental Friendliness: Modern ecoating processes utilize water-based paints that emit fewer volatile organic compounds (VOCs) compared to traditional solvent-based coatings, making them more environmentally friendly.
- Efficient Production: The automated nature of ecoating allows for faster application times, reducing labor costs while maintaining a high-quality finish.
- Versatility: Ecoating is applicable across a wide range of substrates, including steel, aluminum, and plastics, making it suitable for numerous sectors like automotive, aerospace, and appliance manufacturing.
The Importance of Ecoating in the West Midlands
Local Manufacturers and Ecoating Demand
The West Midlands has long been a hub for manufacturing, with a strong focus on automotive and industrial components. As the region continues to evolve, the demand for high-quality finishing processes such as ecoating has surged. Companies are increasingly recognizing the value of durable coatings as they seek to enhance product quality and longevity. The presence of numerous manufacturers in the area looking for reliable coatings partners makes the ecoating west midlands a critical aspect of the regional economy.
Economic Impact of Ecoating Services
The economic implications of ecoating services in the West Midlands are significant. With many local manufacturers relying on ecoating for protective and aesthetic purposes, the growth of such services contributes to job creation and economic dynamism in the area. Investing in ecoating technology not only elevates product quality but also helps companies reduce costs associated with corrosion repairs and maintenance. As firms move towards sustainable practices, ecoating stands at the forefront, reinforcing the local economy’s resilience and competitiveness.
Success Stories from West Midlands Businesses
Numerous businesses in the West Midlands have experienced remarkable transformations through ecoating. For example, a local automotive parts manufacturer reported a significant drop in product returns attributed to rust and finish failure after switching to an ecoating process. By enhancing the durability of their products, they improved customer satisfaction and increased their market share. Similarly, a manufacturer in the construction industry upgraded their coating methods to include ecoating, leading to a 30% increase in product lifespan, solidifying their reputation as a provider of high-quality solutions in their market.
Choosing the Right Ecoating Service Provider
Key Factors to Consider When Selecting a Coating Company
Selecting the right ecoating service provider can greatly influence the success of your coating applications. Several key factors should be considered:
- Experience and Credibility: Look for providers with a solid track record in the industry. Pay attention to their prior projects and customer reviews, as these indicators can give insight into their capabilities.
- Technology and Equipment: Modern ecoating facilities should utilize advanced technology to ensure consistent quality. Investigate whether the provider keeps up with industry trends and innovations.
- Quality of Materials: The type and quality of paint materials used significantly impact the outcome of the coating process. Ensure that the provider uses high-grade, eco-friendly materials.
Evaluating Quality and Reliability in Ecoating Services
Once potential providers have been identified, evaluate their quality and reliability. This can be achieved through:
- Certification and Compliance: Verify that the ecoating service provider meets industry standards and possesses relevant certifications, which ensure adherence to safety and quality regulations.
- Sampling and Testing: Request sample coatings to evaluate their appearance and durability. This firsthand experience can help confirm if their services align with your requirements.
- Post-Service Support: A reliable service provider should offer support after the coating application, including guidance on care and maintenance of the coated surfaces.
Customer Testimonials and Case Studies
Customer testimonials serve as powerful endorsements of a provider’s reliability and success. Case studies showcasing how a specific ecoating service solved challenges for a client can provide valuable insights into the provider’s capabilities. Look for case studies that reflect your industry’s specific needs and challenges, as this context can demonstrate the provider’s expertise and understanding of your requirements.
Best Practices for Ecoating: Tips for Optimal Results
Preparation and Pre-treatment for Ecoating
Preparation is crucial for achieving optimal results with ecoating. The success of the coating largely depends on how well the substrate is prepared. Effective pre-treatment steps include:
- Cleaning: Remove all contaminants, such as dirt, oils, and grease, from the substrate using appropriate cleaning solutions.
- Surface Profiling: For metal surfaces, creating a rough profile can enhance adhesion. Techniques such as sandblasting or using chemical etching can be effective.
- Dehumidification: Ensure that the coating environment is controlled for humidity, as moisture can negatively affect coating adhesion and quality.
Post-treatment Guidelines to Enhance Durability
Once the ecoating process is complete, several post-treatment actions can enhance the durability and effectiveness of the coating:
- Curing: Many ecoatings require a curing process to achieve maximum hardness and resilience. Follow manufacturer guidelines for necessary curing times and temperatures.
- Inspection: Conduct thorough inspections to catch any defects after coating but before shipping. Early detection can save costs and enhance customer satisfaction.
- Storage Conditions: Store finished products in controlled environments to avoid exposure to elements that could compromise the coating’s integrity.
Maintaining Ecoated Surfaces Over Time
Maintaining ecoated surfaces is essential for ensuring their longevity and performance. Regular maintenance should include:
- Routine Cleaning: Clean coated surfaces regularly with non-abrasive cleaning agents to maintain aesthetics and prevent accumulation of contaminants.
- Inspections for Damage: Regularly inspect ecoated surfaces for signs of wear, scratches, or corrosion to address potential issues proactively.
- Touch-Up Kits: Consider providing touch-up kits for minor repairs that might be necessary on large coated surfaces.
The Future of Ecoating Technologies
Innovations and Trends in Ecoating
The ecoating industry is poised for significant innovations that will enhance performance and sustainability. Emerging trends include:
- Smart Coatings: The future may see the development of smart ecoatings that can change properties in response to environmental conditions, providing even more sophisticated protection.
- Advanced Automation: As businesses seek efficiency, the integration of automation and robotics into ecoating processes is expected, improving speed and precision.
- Custom Coating Solutions: Tailored ecoating solutions that meet specific customer requirements are likely to become more prevalent, enabling companies to differentiate their products effectively.
Environmental Considerations and Eco-friendly Practices
As industries increasingly prioritize sustainability, ecoating technologies must evolve to meet these expectations. Key environmental considerations include:
- Low-VOC and Water-Based Formulations: The move toward low-VOC and fully water-based formulations continues to grow, aligning with global sustainability standards and regulations.
- Recycling and Waste Minimization: Processes that incorporate recycling of unused paint particles and minimize waste during ecoating can enhance environmental stewardship.
- Energy Efficiency: Investing in energy-efficient equipment can further reduce the environmental footprint of the ecoating process.
Predictions for the Ecoating Industry in the West Midlands
Looking ahead, the ecoating industry in the West Midlands appears set for considerable growth. With local manufacturers increasingly embracing these technologies, the region may be uniquely positioned to lead in innovative coating applications. As sustainability becomes a non-negotiable aspect of business, ecoating’s role in enhancing product durability while protecting the environment will be pivotal in shaping future manufacturing processes.